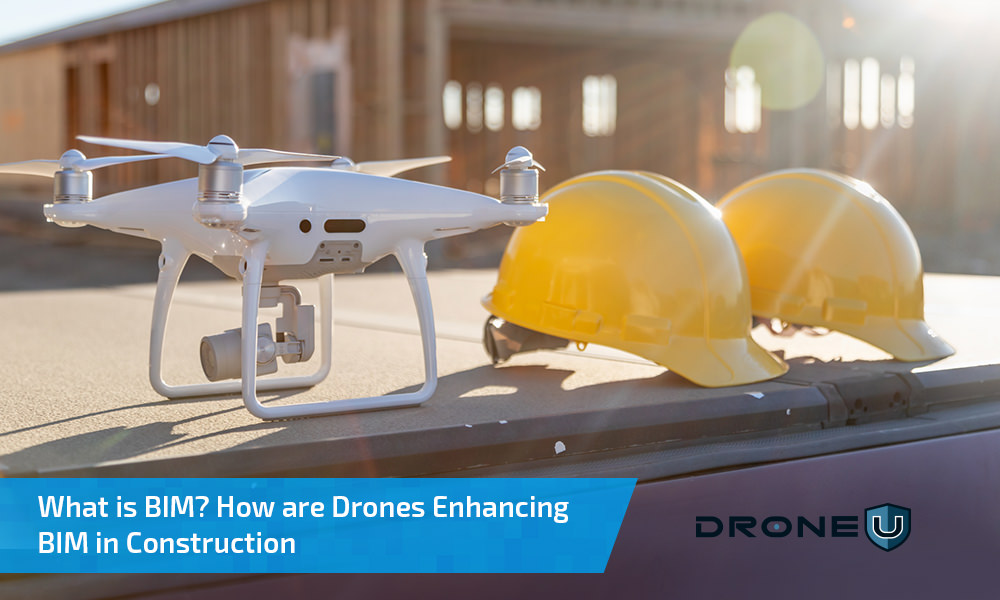
How can Drones in Construction Enhance the BIM Workflow?
Drones are offering a new perspective for BIM (Building Information Modeling) across the entire construction life-cycle. From as-builts to facility management and compliance, drones are quickly providing more data and solving efficiency problems once unnoticed.
What is BIM?
BIM or building information modeling is a project management technique which allows information to flow across the entire construction process seamlessly. BIM will enable companies to visualize every aspect of the project in 3d space, from plumbing to electric. While the systems haven’t provided the most lifelike models, they help reduce document errors and omissions. Also, a BIM model reduces re-work, increases scheduling efficiency, and reduces claims & litigation.
The purpose of BIM is to break down obstacles that prevent stakeholders in a construction project to access information in real time.
What are BIM Objects?
BIM Objects are the building blocks of a BIM model. Modelers can drag and drop BIM Objects from an extensive Library, and create a model without actually going through the hassle of actually building one.
BIM Objects mimic real-life products, not only dimensionally but also functionally.
This ability to capture information can be incredibly powerful, prevent design changes, and reduce the likelihood of construction disputes and litigation.
Using Building Information Modeling, it is possible to engineer the most optimum design at the first go with every system necessary for permits to completion. The ability to access manufacturer-stated product information allows for greater collaboration between the designer and the manufacturer and dramatically helps in model optimization.
Remember, BIM is a constant and iterative process.
What are Some Applications of Drones in Construction? How are Drones enhancing BIM Models?
The construction industry loves drones. The proof is in the pudding as the usage of drones in construction has skyrocketed for engineers, construction companies and even surveyors. Drones aid in construction in so many ways. Remember, drones don’t just take pictures, they can also take measurements from pictures or photogrammetry.
Building Information Modeling is a visualization of the size, scale, and functionality of all systems in a building. Drones take this computer-aided design and overlay real-world lifelike 3d models to ensure accurate construction from the plans. It is like a remote site audit.
From the start of a project, drones are used for a permanent record of construction in addition to remote viewing and compliance review. While drones have been great for ensuring work completion and quality, they also aid in precise ways over the life cycle. When the project starts and elevations need to be taken, typically surveyors are called in to get accurate measurements to accurately understand where to lay the foundation and understand where property lines end. Drones are even being used for the ALTA surveys that are used in pre-construction.
Drones in construction are also used to measure the amount of cut and fill to accomplish to create a level foundation. From there, drones can help aid in creating 3D lifelike models via photogrammetry software.
Drone in Construction – Different Uses
1. Drone Surveying: From ALTA Surveys to Basic Elevations
2. Simulation: 3D Remote Reconstruction
3. Site Planning & Safety Compliance
4. Construction Marketing & Hyper-lapses
5. Project Coordination
6. Facility Management
Drone Surveying
When GPS came to the market, surveyors were the last in line to adopt the new technology. Now it is a stark contrast to the modern day job site fueled by aerial insights and powered by autonomous vehicles. Now drones can capture survey grade GPS and marry that data with images to create survey grade photogrammetry and maps. Toys have transformed into tools to gather survey grade data at a lower fixed cost and opportunity cost. (time saved)
Check out our recent podcast on ADU to learn how to incorporate the most accurate and cost-effective drone mapping workflow for your construction site.
Drones in construction can capture survey data directly on site, process on site, and then communicate to driverless bulldozers and excavators.
Construction Simulation
Once construction is underway, we can create 3d lifelike models and merge that map with our BIM data. Contractors and engineers can simulate real-life conditions and audit existing development. They can now view the internal environment and the external environment in one seamless workflow.
So, for instance, using Building Information Modeling, you can quickly determine if a building meets the designed energy efficiency standards like LEED. Utilizing BIM documentation, we can view what was planned and what has been completed on one screen, we can even test new materials and their effect on the environment surrounding the material.
Site Planning & Safety
While aerial surveys can help to plan site layout that results in safe and efficient operation. 3D Models created from drones can help managers determine the placement of equipment, personnel, and vital raw materials. While these models “show” the site, they can also measure the site and the materials.
Drones in construction help audit raw materials, aggregates, and more. These models showcase volumetric measurements to have an accurate understanding of how much material you may need, how much you used, and how much you paid for. This process to audit these materials is much faster and more efficient than hand measurements that are currently used.
Construction Progress Monitoring
Let’s be clear. To build an information-rich BIM model and lifelike 3D drone model, you need to adopt rigorous systems and processes that would seem quite overwhelming initially. Implementing Building Information Modeling will also require extensive training of site and managerial staff as well. You don’t know how to solve efficiency problems when you don’t know they exist.
To model construction progress, companies are utilizing RFID tags. The entire project needs to be divided into tiny grids or sub-components, each with an RFID tag. By doing so, the minutest of tasks can be closely monitored by a construction manager.
For prefabricated structures, progress monitoring can start much earlier, during the manufacturing phase itself. Once a structure is manufactured and being transported to the site, movement can also be monitored closely. And finally, once a structure is installed on-site, this progress can be documented in a centralized information system.
For on-site processes like fabrication and concreting, completion of a task can be easily documented in real-time. Moreover, drones like the Mavic 2 Enterprise are equipped with speakers which can allow a site supervisor to communicate with the construction crew easily. (As long as they don’t fly over their crew)
On reading an RFID tag, a construction manager can instantly access the following information:
o Manufacturing Date
o Date of Shipping
o Installation Date
o Product information provided by the manufacturer
Having manufacturer-stated product information on your finger-tips (literally) greatly decreases the likelihood of expensive change orders. Typically, project managers, supervisors, and crew members using card readers fitted to iPad’s, smartphones or tablets to document the progress. However, now, with drone technology, you can replace a time-consuming process with an efficient one.
Using Drone-mounted RFID technology, construction managers can now monitor and document site progress far more quickly. MIT has also devised an ingenious solution which eliminates the need for drones to carry bulky card-readers. A lighter payload would mean longer flight-time and reduced flying cost.
Another creative solution for comparing design and as-built conditions is the Pix4D crane camera. Mounted on a tower crane’s jib, construction managers can now get a bird’s eye view of the site. This product is beneficial for sites that butt up to airports and have flight restrictions. 3D point clouds and 3D mesh models are wirelessly uploaded to Pix4DBIMCloud.
Construction Marketing & Hyperlapses
When 3D models, created by drones, are created regularly, pilots can create video motions around those models to create a hyper-lapse of the project area. This hyper-lapse is a moving time-lapse around the construction site. You can literally “animate” the site being built, without having to pay for a costly animation.
Let’s discuss site coordination first, a large-scale construction site typically involved owner, investors, manager designers, civil engineers, architects, and hundreds of subcontractors. Every sub-contractor should be able to visualize how their piece of the puzzle and how their work allows the rest of the puzzle to come together.
Construction marketing may be the lowest hanging fruit and easiest utilization of drones. From marketing photos that once showed compliance, are now used to market service by subcontractors. Preparing a hyper-lapse for pitching a project to prospective investors doesn’t require a BIM model, but it does require a comprehensive knowledge of drone mapping and 3d textured meshes!
Facility Management
After project closeout, drones are extremely useful and time efficient to conduct building inspections. Drones with zoom and thermal cameras aid in capturing greater insights and greater problems. Inspection data can be fed online so stakeholders can remotely view data at the click of a button. Thermal cameras can even showcase machines that are properly functioning or not!
Become a Drone U Member.
Do not forget to subscribe and listen to Ask Drone U, the #1 drone podcast on iTunes!
Add Your Comment