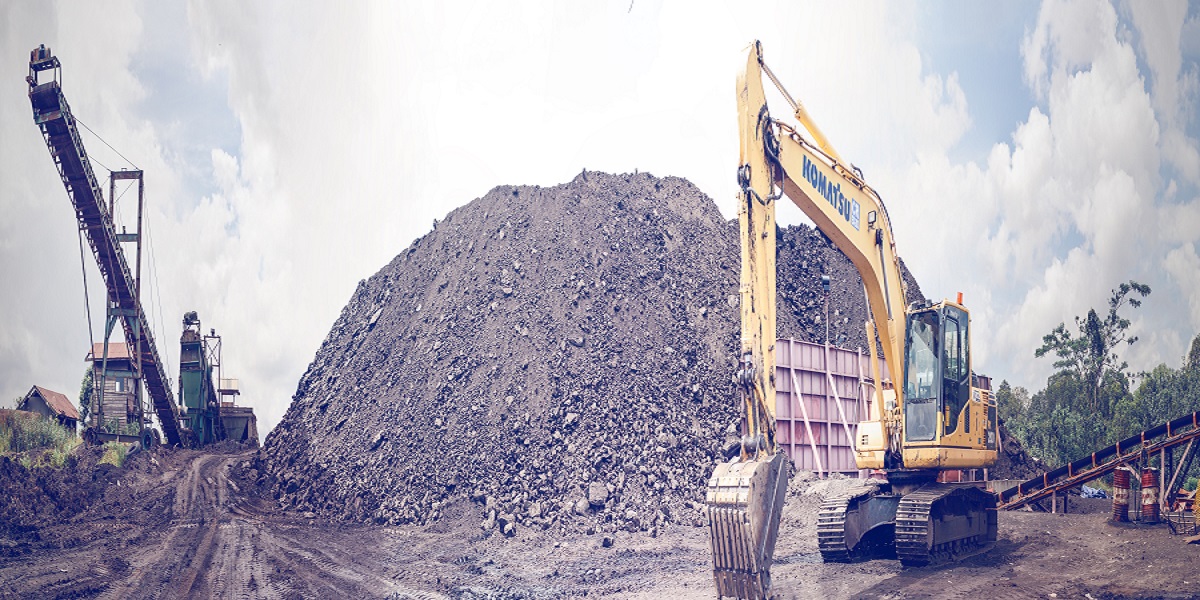
In this blog post I explore how drones can be put to use in the mining and metals industry. Mining and metals is a hazardous industry. In spite of technological advancements, site accidents are still commonplace. So, how can drones help bring about site safety in the mining industry? And can they add to a company’s bottom-line? Can drones be used to inspect mining equipment in confined places? We also discuss how 3D mapping can help supervise stockpile inventories and conduct pre-blast and post-blast analysis.
Drone Monitoring of Mining Sites for Increased Operational Safety
Rio Tinto is the third largest mining company in the world. Headquartered in United Kingdom, Rio Tinto has more than 50,000 employees on its rolls. In 2017, this corporate behemoth managed to cross revenues of $45 billion. Even with its vast repertoire or resources, Rio Tinto has experienced niggling problems in one area – Safety.
“Rio Tinto heavily blamed by protesters over 41 mine worker deaths” – 15th April, 2014 in The Guardian
“Death at Rio Tinto mine site in the Pilbara” – 4th July, 2017 in The Border Mail
“Rio Tinto declares force majeure at Kennecott following fatal accident” – October 17, 2017 in Mining.com
Drones can help mining companies in their endeavor to bring about site safety. Let us talk about site monitoring or site surveying. A drone pilot can fly a drone close enough to look for any sign of dilation’s or cracks. And a drone can easily access hard to reach areas also. Along with GPS monitoring, drones can help miners and technologists precisely determine if a crack crosses a certain threshold. The cost of a GPS scanner is a whopping $180,000. Whereas a drone system (capable of doing this job) will cost you somewhere around $20,000.
Once miners receive this data, the mine section can be shut off to allow for runoff. Using a zoom camera like Zenmuse Z30 can enable them to see the minutest of details from afar. This helps miners collect data for events like landslides without being close to risky areas.
Using a drone is also a quick and cost effective way to making sure that all employees have been evacuated from the mining site before a blast. BHP has been using drones for its Queensland mines. And this has worked out to be significantly cheaper. Replacing planes with drones has resulted in savings to the tune of Australian $5 million per year. Renting a plane would cost BHP $2,000 per hour. Whereas, a UAV pilot can be hired for $200 per hour.
Site monitoring with drones also helps ensure compliance of safety practices . Drone footage can also be used to create safety training videos for employees
“Things just got a lot safer at Kennecott’s copper pit thanks to something no bigger than a back pack” – ABC News
How to Use Drones for Mining Equipment Inspections
Mining equipment inspection is a hazardous and costly operation. Eric Romersa of WS Data 3D, a mining inspection company estimates that a mining inspection can cost as much as $150,000. A typical mining inspection will last for an hour and all production comes to a complete halt till inspection is over.
These inspections are tedious operations. Protective scaffolding needs to be constructed. And it may require a team of skilled people wearing special suits to conduct a mining inspection. Moreover they need to adhere to a strict timeline. (Beyond which risk to human life increases exponentially) Because of this, the inspection team is in a hurry to get in and out. And hence, the quality of data might leave a lot to be desired.
Using drones, these inspections can be conducted from outside the hazardous area. Thus, data captured with a drone will be far better than that captured by a human.
Note that special collision proof drones need to be used for conducting inspection in confined spaces. Elios is one such drone capable of carrying out such critical inspections. Check out this cool video which shows an ongoing inspection. Typical mining equipment that needs to be inspected includes conveyor belts, bridges, roads and towers.
Putting 3D Mapping to Use in Mining
“Information will be the single biggest differentiating factor between the mining operations of the past and those in the future, and drones can produce a wealth of information to allow us to make better decisions.” – Rio Tinto head of technology and innovation, Greg Lilleyman
Site monitoring using 3D drone maps and models is another potential application. A 3D model makes it possible to look at the mine from all possible angles. Creating a 3D drone map before a blast and after a blast helps miners get quick and accurate production updates. Using Point Cloud and a software like AutoCad or SolidWorks, miners can accurately make measurements for pre and post blast data. And these can also be fed into mining equipment to automate movement. This ensures that production targets are achieved to a high degree of accuracy.
Using 3D mapping for making stockpile measurements in mining has become a standard industry practice. According to Pix4D, using drones has helped the top mining companies calculate their stockpile inventories to an accuracy of 2-5%. Because this is a quick and cost effective process, miners can measures their inventories more often. And this can help them plan productions in a more efficient manner.
Conclusion
Photogrammetry as well as 3D mapping can be useful in making mining safer and more profitable. Reduced human intervention and the possibility of replacing capital heavy equipment renders drones an extremely attractive solution for the mining industry.
Check out our Medium page for more such content
Do not forget to subscribe and Listen to Ask Drone U, the #1 drone podcast
Connect with a vibrant drone community by becoming a Drone U member
Add Your Comment